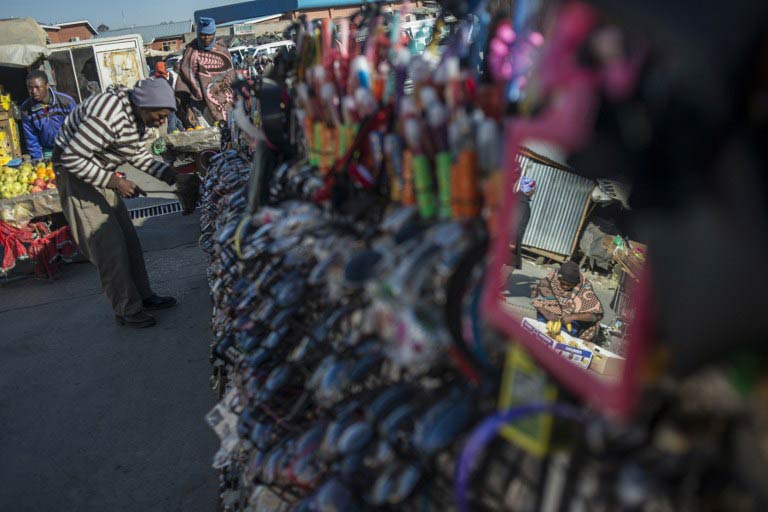
I am standing outside the gates of a textile factory in the Industrial Area of Maseru West. The midday sun is blaring, and the air is heavy with waiting. In ten or so minutes, at precisely 11.45am, the factory workers inside the gates will get their one-hour lunch break. Outside the gates, preparations are underway. On the concrete ground, in between puddles of dirty water, several street vendors are setting up. A woman has laid out a blanket and is arranging piles of peaches onto it. A man is heaping stacks of processed meat onto a small cooker. Somebody has botched an attempt to light a fire inside a cardboard box. The flames consume the cardboard, sending thick smoke rising into the air. Next to a wall lined with barbed wire, groups of women are seated on the only patch of grass in sight. Some have brought umbrellas to shield themselves from the harsh sun. They too are waiting, hoping to find work inside the gates.
Lesotho’s apparel and textile industry is one of the largest in Africa. This particular factory employs approximately 4 000 people, the majority of whom are women. In a country with an overall unemployment rate of 26%, the industry employs close to 40 000 people in 40 factories, providing more than 80% of Lesotho’s manufacturing employment. The majority of the garments produced in the country are for major US brands such as Gap Inc., Levi Strauss and Wal-Mart.
Since 2008, Lesotho’s government and apparel manufacturers have worked hard to market Lesotho as a ‘responsible sourcing destination’ for ‘ethical consumers’. In a nutshell, this means that textile factories in the country have to adhere to Lesotho’s labour legislation, which enshrines the International Labour Organisation’s (ILO) core conventions. These include no child or forced labour, payment of minimum wages, regulated maximum working hours and ensuring that basic requirements for health and safety are met. The major brands that source their products from Lesotho also monitor factories to ensure that working conditions meet their codes of conduct.
I am standing with ‘Mareitumetse Mokhoro, who works for the Lesotho Clothing and Allied Workers’ Union (Lecawu), a trade union that advocates for better wages and working conditions for factory workers in Lesotho. In cases of mistreatment, Lecawu offers legal assistance by representing workers in court. Mokhoro is also waiting. Lunchtime is the only time she can meet with workers.
‘Oppressed and underpaid’
“Factory workers in Lesotho are oppressed and underpaid,” Mokhoro tells me. “They receive the minimum wage, but this isn’t enough. They are often insulted or treated badly. Most of the cases that we deal with are unfair dismissals or underpayments.”
The workers in this factory receive a monthly salary of R1 212, for nine hours of work a day, five days a week. This amounts to less than R7 an hour. I find it hard to imagine how anyone survives on such a salary, especially people who have a family to support.
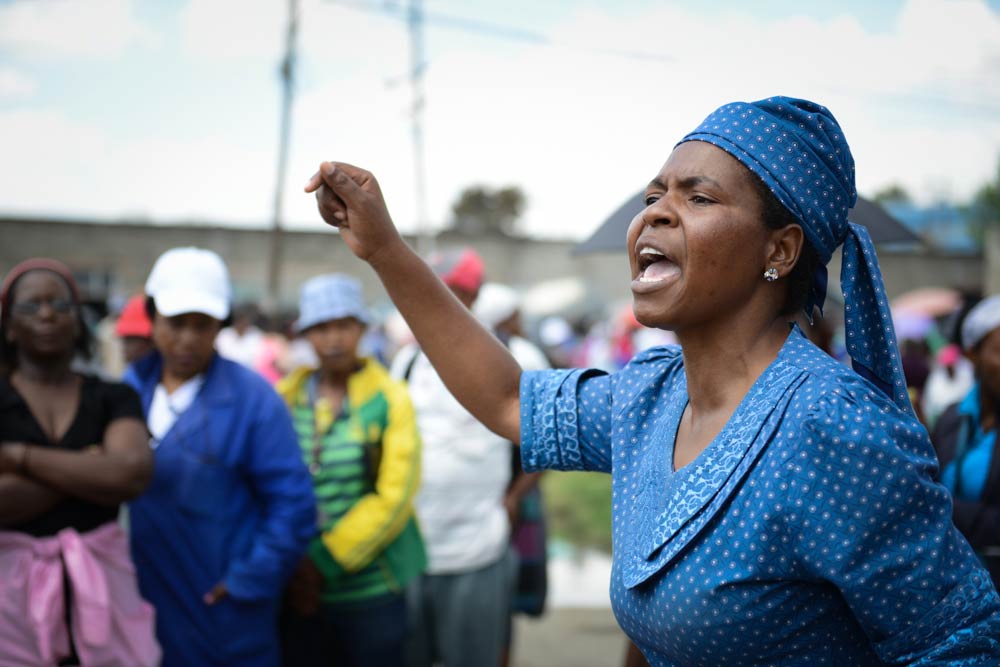
“Half a loaf is better than no loaf,” says Mokhoro wryly. “You know, women in Lesotho are very strong. Most factory workers do not have husbands, and they earn very little money. But still, they are able to build houses and send their children to school. Even if they are poor, they don’t give up.”
Before becoming a full-time employee of Lecawu, Mokhoro spent eight years working in a textile factory.
“As a factory worker, I was treated badly by my employers because I spoke out about the problems that workers face,” she explains. “So I decided to fight outside of the company, so that management has no control over me. Now I have a voice. I can openly say: workers are mistreated.”
“Some employers are willing to work with Lecawu, but others are hostile, and they don’t allow us to come into the factories and solve problems. We always refer cases to the courts, but these cases take a long time to be resolved. That discourages the workers.”
At 11.45, a bell rings from inside the factory and the gates open. The workers stream out, walking fast. The quiet, waiting atmosphere has instantaneously transformed into a hurrying, crowded bustle of noise and activity. Mokhoro is standing a few metres from the gates, shouting out to the workers, appealing to them to listen to what she has to say. For a good 20 minutes she receives very little response. The vendors who have been setting up are inundated. I watch as the workers walk back towards the gates, some of them clutching plastic bags of greasy chips, fat cakes and cheap, processed meat sausages. Some have brought lunch boxes with them and are hungrily tucking in. Gradually, 50 or so workers gather in a circle around Mokhoro.
I look at the weary expressions on their faces as they listen to her. Mokhoro punches her fist into the air regularly and shouts out several call-and-response slogans that are answered by a few of the onlookers. Many of them simply stand still and silent.
“What kinds of troubles do you face as workers?” she asks the group.
“We don’t earn enough money.”
“We’re hungry.”
“We have to rent small rooms.”
“We have to walk. We don’t have the money for transport.”
“Sometimes we are mistreated if we don’t understand instructions.”
“I eat only papa and cabbage!” says one woman standing close to me, pushing her plastic lunch box forward to display its contents.
For 30 minutes, Mokhoro speaks to the workers, listening to their complaints and concerns, and encouraging them to convince others to join Lecawu. With 3 800 members in 21 factories, the union has a strong presence, but in many factories it does not yet have enough members to legally bargain and negotiate with employers.
At 12.45, the bell sounds again, and the gates to the factory begin to close. The factory workers move swiftly, rushing inside, clearly frightened of the possible repercussions of being late. The ground is now littered with small plastic bags. A few of the vendors are packing up to leave. The women seated on the grass remain where they are, waiting.
Leila Hall is a freelance writer living and working in Lesotho.